Wie allgemein bekannt ist, handelt es sich bei einem Sterilisator um einen geschlossenen Druckbehälter, der üblicherweise aus Edelstahl oder Kohlenstoffstahl gefertigt ist. In China sind rund 2,3 Millionen Druckbehälter im Einsatz. Besonders häufig ist dabei die Metallkorrosion, die zu einem Haupthindernis und Ausfallfaktor für den langfristigen, stabilen Betrieb von Druckbehältern geworden ist. Da es sich um einen Druckbehälter handelt, dürfen Herstellung, Nutzung, Wartung und Inspektion des Sterilisators nicht außer Acht gelassen werden. Aufgrund des komplexen Korrosionsphänomens und -mechanismus variieren die Formen und Eigenschaften der Metallkorrosion je nach Material, Umweltfaktoren und Spannungszuständen. Im Folgenden betrachten wir einige häufige Korrosionsphänomene bei Druckbehältern:
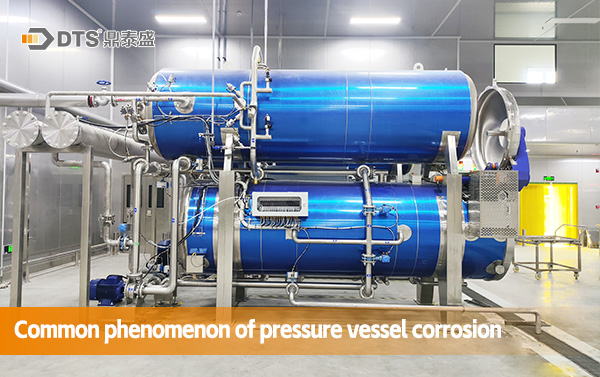
1. Flächenkorrosion (auch als Flächenkorrosion bekannt), ein Phänomen, das durch chemische oder elektrochemische Korrosion verursacht wird. Das korrosive Medium kann alle Teile der Metalloberfläche gleichmäßig erreichen, sodass die Metallzusammensetzung und -anordnung relativ gleichmäßig sind und die gesamte Metalloberfläche gleichmäßig korrodiert. Bei Edelstahldruckbehältern kann sich in korrosiver Umgebung mit niedrigem pH-Wert die Passivierungsschicht auflösen und ihre Schutzwirkung verlieren, was zu Flächenkorrosion führt. Unabhängig von der Flächenkorrosion durch chemische oder elektrochemische Korrosion ist die Bildung einer schützenden Passivierungsschicht auf der Materialoberfläche während des Korrosionsprozesses schwierig. Die Korrosionsprodukte können sich im Medium auflösen oder lose, poröse Oxide bilden, die den Korrosionsprozess verstärken. Die Schäden durch Flächenkorrosion sind nicht zu unterschätzen: Erstens führt sie zu einer Verringerung der Druckfläche des Druckbehälterlagerelements, was zu Perforationen und Undichtigkeiten oder aufgrund unzureichender Festigkeit sogar zu Brüchen oder Ausschuss führen kann. Zweitens wird der Prozess der elektrochemischen, umfassenden Korrosion oft von einer H+-Reduktionsreaktion begleitet, die dazu führen kann, dass sich das Material mit Wasserstoff füllt, was dann zu Wasserstoffversprödung und anderen Problemen führt, was auch der Grund ist, warum die Ausrüstung während der Schweißwartung dehydriert werden muss.
2. Lochfraß ist ein lokales Korrosionsphänomen, das an der Metalloberfläche beginnt und sich nach innen ausbreitet und kleine, lochförmige Korrosionsgruben bildet. In bestimmten Umgebungen können nach einiger Zeit einzelne geätzte Löcher oder Lochfraß an der Metalloberfläche auftreten, die sich mit der Zeit immer weiter in die Tiefe ausbreiten. Obwohl der anfängliche Metallgewichtsverlust gering sein kann, werden aufgrund der schnellen lokalen Korrosion häufig Geräte und Rohrwände perforiert, was zu plötzlichen Unfällen führt. Lochfraß ist schwer zu erkennen, da die Lochfraßlöcher klein sind und oft von Korrosionsprodukten bedeckt sind. Daher ist es schwierig, den Lochfraßgrad quantitativ zu messen und zu vergleichen. Daher kann Lochfraß als eine der zerstörerischsten und heimtückischsten Korrosionsformen angesehen werden.
3. Intergranulare Korrosion ist ein lokales Korrosionsphänomen, das entlang oder in der Nähe der Korngrenze auftritt. Es ist hauptsächlich auf Unterschiede zwischen der Kornoberfläche und der inneren chemischen Zusammensetzung sowie auf das Vorhandensein von Korngrenzenverunreinigungen oder inneren Spannungen zurückzuführen. Obwohl intergranulare Korrosion auf Makroebene möglicherweise nicht offensichtlich ist, geht die Festigkeit des Materials, sobald sie auftritt, fast augenblicklich verloren, was häufig zu einem plötzlichen Ausfall der Ausrüstung ohne Vorwarnung führt. Im Ernst, intergranulare Korrosion wandelt sich leicht in intergranulare Spannungsrisskorrosion um, die wiederum zur Ursache von Spannungsrisskorrosion wird.
4. Spaltkorrosion ist ein Korrosionsphänomen, das in engen Spalten (üblicherweise 0,02–0,1 mm breit) auftritt, die durch Fremdkörper oder aus strukturellen Gründen auf einer Metalloberfläche entstehen. Diese Spalten müssen eng genug sein, damit Flüssigkeit einströmen und stehen bleiben kann, wodurch Korrosion im Spalt entsteht. In der Praxis können Flanschverbindungen, Mutternpressflächen, Überlappverbindungen, nicht durchgeschweißte Schweißnähte, Risse, Oberflächenporen, nicht gereinigte Schweißschlacke, die sich auf der Metalloberfläche des Zunders ablagert, Verunreinigungen usw. Spalten bilden und Spaltkorrosion verursachen. Diese Form lokaler Korrosion kommt häufig vor und ist äußerst zerstörerisch. Sie kann die Integrität mechanischer Verbindungen und die Dichtheit von Geräten beeinträchtigen und zu Geräteausfällen oder sogar Unfällen führen. Daher ist die Vorbeugung und Kontrolle von Spaltkorrosion sehr wichtig, und regelmäßige Wartung und Reinigung der Geräte sind unerlässlich.
5. Spannungsrisskorrosion macht 49 % aller Korrosionsarten an Behältern aus. Sie ist durch die synergistische Wirkung von gerichteter Spannung und korrosivem Medium gekennzeichnet und führt zu spröder Rissbildung. Diese Art von Riss kann nicht nur entlang der Korngrenze, sondern auch durch das Korn selbst entstehen. Tiefe Risse im Inneren des Metalls führen zu einem deutlichen Festigkeitsverlust der Metallstruktur und können sogar zu plötzlichen, unvorhergesehenen Schäden an Metallgeräten führen. Spannungsrisskorrosion (SCC) ist daher eine plötzliche und starke Zerstörungskraft. Sobald der Riss entsteht, breitet er sich sehr schnell aus, ohne dass es vor dem Versagen eine nennenswerte Vorwarnung gibt. Dies ist eine sehr gefährliche Form von Geräteversagen.
6. Das letzte häufige Korrosionsphänomen ist die Ermüdungskorrosion. Dabei handelt es sich um den Prozess der allmählichen Beschädigung der Materialoberfläche bis hin zum Bruch durch die kombinierte Einwirkung von Wechselspannung und korrosiven Medien. Die kombinierte Wirkung von Korrosion und Materialwechselspannung verkürzt die Entstehungszeit und die Zykluszeiten von Ermüdungsrissen deutlich und erhöht die Rissausbreitungsgeschwindigkeit, was die Dauerfestigkeit von Metallwerkstoffen stark reduziert. Dieses Phänomen beschleunigt nicht nur den vorzeitigen Ausfall des Druckelements des Geräts, sondern verringert auch die Lebensdauer des nach Ermüdungskriterien ausgelegten Druckbehälters deutlich. Um verschiedenen Korrosionsphänomenen wie Ermüdungskorrosion an Edelstahldruckbehältern vorzubeugen, sollten während des Betriebs folgende Maßnahmen ergriffen werden: Sterilisationstanks, Warmwasserspeicher und andere Geräte innen alle 6 Monate gründlich reinigen; bei hoher Wasserhärte und einer täglichen Betriebsdauer von mehr als 8 Stunden alle 3 Monate reinigen.
Veröffentlichungszeit: 19. November 2024